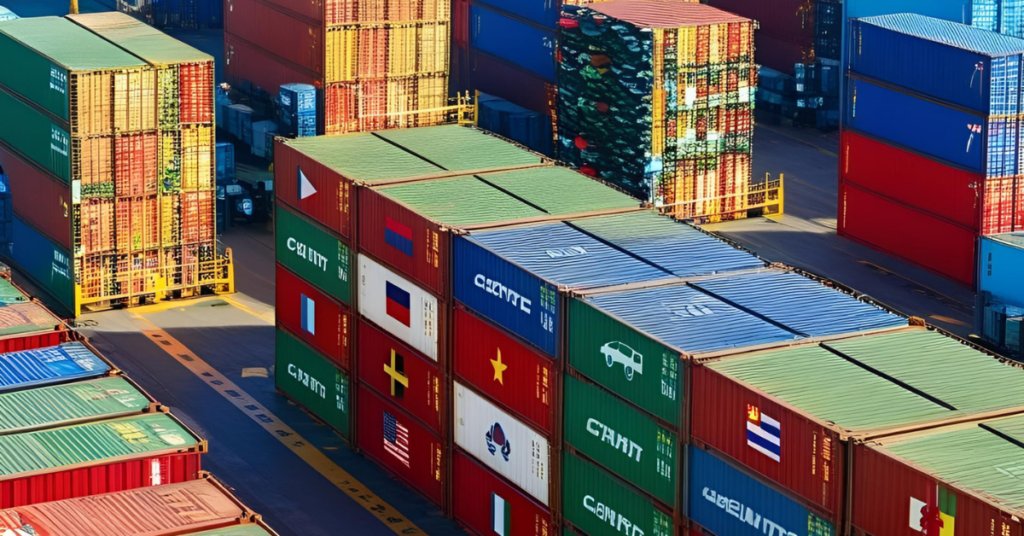
As debate over domestic manufacturing intensifies, the U.S. auto industry is facing a sobering reality: building a 100% “Made in the USA” vehicle is becoming nearly impossible in today’s interconnected economy. While political rhetoric often pushes for fully American-made products, industry insiders acknowledge that the global supply chain has become both a strength and a vulnerability.
Key components—such as lithium-ion batteries, semiconductor chips, and precision electronics—are sourced from countries like China, South Korea, Japan, and Mexico. Despite being assembled in American factories, most modern vehicles are the result of a collaborative international effort, reflecting decades of economic interdependence.
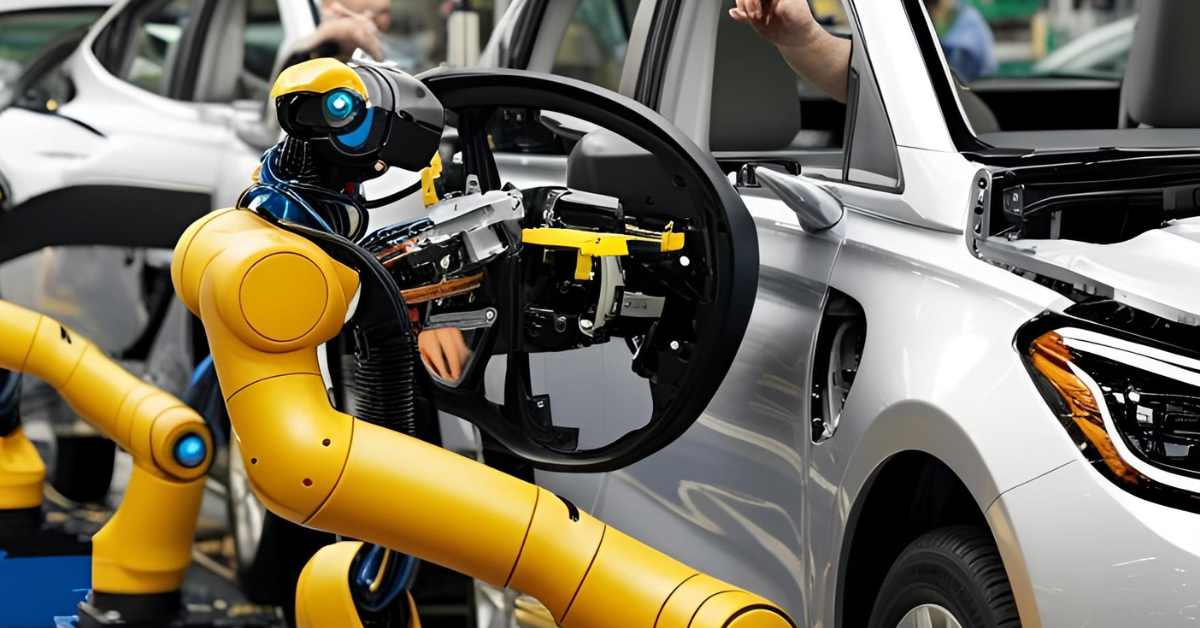
The recent imposition of tariffs on non-U.S.-made cars and automotive parts has sparked concern across the industry. While intended to stimulate local production, these measures have raised manufacturing costs, disrupted timelines, and strained U.S.-based plants that still rely on foreign-made inputs.
According to analysts, this protectionist approach may hurt more than it helps, especially in an industry already adapting to the electric vehicle (EV) revolution. Many EV components are not yet produced at scale in the U.S., making localization both aspirational and expensive.
Consumers are also caught in the middle. Prices for new vehicles—already high due to pandemic-era shortages—continue to rise, and wait times for repairs are stretching due to part delays and costlier imports.
However, some automakers are responding with investment. Companies like Ford and GM are retooling factories, building battery plants, and investing in U.S.-based supply chains, particularly in the Midwest and the South. But experts warn: full independence from global sourcing is unlikely—at least in the near term.
The U.S. auto sector, once the poster child of American industrial might, now stands as a reflection of the global economy’s complexity—where “Made in America” is often the final touch, not the full story.
The recent imposition of tariffs on non-U.S.-made cars and automotive parts has sparked concern across the industry. While intended to stimulate local production, these measures have raised manufacturing costs, disrupted timelines, and strained U.S.-based plants that still rely on foreign-made inputs.
According to analysts, this protectionist approach may hurt more than it helps, especially in an industry already adapting to the electric vehicle (EV) revolution. Many EV components are not yet produced at scale in the U.S., making localization both aspirational and expensive.
Consumers are also caught in the middle. Prices for new vehicles—already high due to pandemic-era shortages—continue to rise, and wait times for repairs are stretching due to part delays and costlier imports.
However, some automakers are responding with investment. Companies like Ford and GM are retooling factories, building battery plants, and investing in U.S.-based supply chains, particularly in the Midwest and the South. But experts warn: full independence from global sourcing is unlikely—at least in the near term.
The U.S. auto sector, once the poster child of American industrial might, now stands as a reflection of the global economy’s complexity—where “Made in America” is often the final touch, not the full story.
The recent imposition of tariffs on non-U.S.-made cars and automotive parts has sparked concern across the industry. While intended to stimulate local production, these measures have raised manufacturing costs, disrupted timelines, and strained U.S.-based plants that still rely on foreign-made inputs.
According to analysts, this protectionist approach may hurt more than it helps, especially in an industry already adapting to the electric vehicle (EV) revolution. Many EV components are not yet produced at scale in the U.S., making localization both aspirational and expensive.
Consumers are also caught in the middle. Prices for new vehicles—already high due to pandemic-era shortages—continue to rise, and wait times for repairs are stretching due to part delays and costlier imports.
However, some automakers are responding with investment. Companies like Ford and GM are retooling factories, building battery plants, and investing in U.S.-based supply chains, particularly in the Midwest and the South. But experts warn: full independence from global sourcing is unlikely—at least in the near term.
The U.S. auto sector, once the poster child of American industrial might, now stands as a reflection of the global economy’s complexity—where “Made in America” is often the final touch, not the full story.
The recent imposition of tariffs on non-U.S.-made cars and automotive parts has sparked concern across the industry. While intended to stimulate local production, these measures have raised manufacturing costs, disrupted timelines, and strained U.S.-based plants that still rely on foreign-made inputs.
According to analysts, this protectionist approach may hurt more than it helps, especially in an industry already adapting to the electric vehicle (EV) revolution. Many EV components are not yet produced at scale in the U.S., making localization both aspirational and expensive.
Consumers are also caught in the middle. Prices for new vehicles—already high due to pandemic-era shortages—continue to rise, and wait times for repairs are stretching due to part delays and costlier imports.
However, some automakers are responding with investment. Companies like Ford and GM are retooling factories, building battery plants, and investing in U.S.-based supply chains, particularly in the Midwest and the South. But experts warn: full independence from global sourcing is unlikely—at least in the near term.
The U.S. auto sector, once the poster child of American industrial might, now stands as a reflection of the global economy’s complexity—where “Made in America” is often the final touch, not the full story.